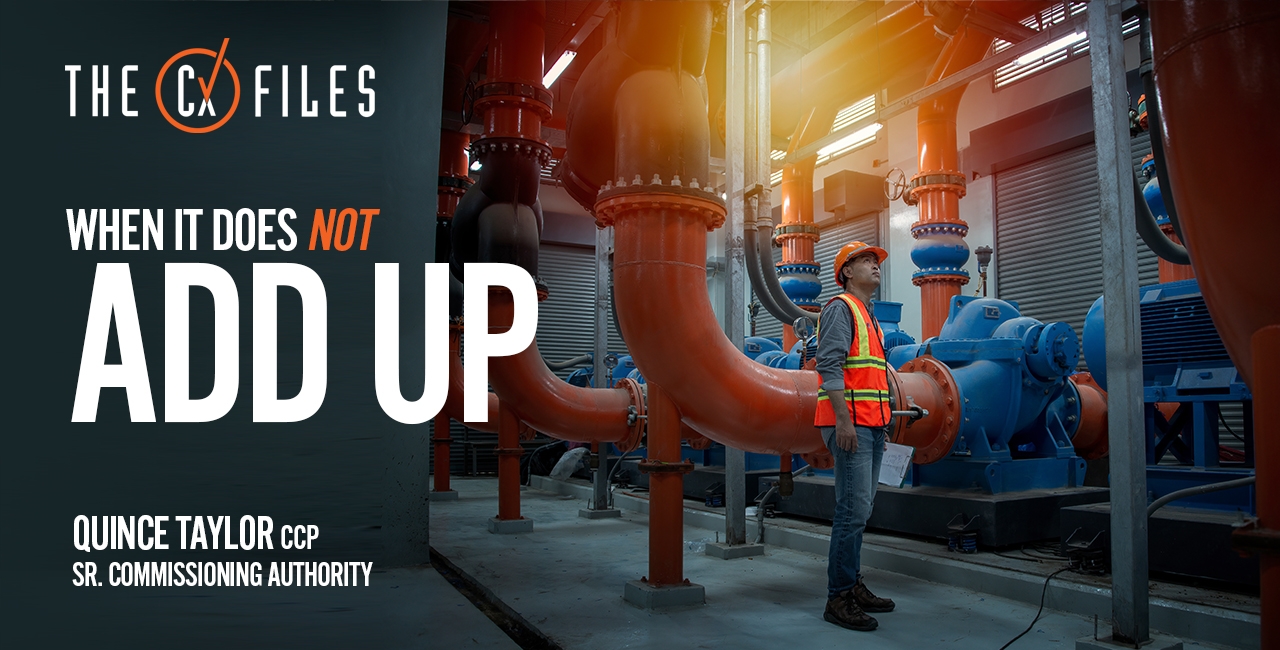
The Cx Files
Chapter 3: When it Does Not Add Up
Jun 16, 2022
Quince Taylor, CCP
The Commissioning (Cx) team performed forensic detective work on a chilled water (CHW) system. The CHW system measurements reflected a high volume of water leaving the CHW pump and too little CHW at a large number of individual HVAC units. The water leaving the pump must equal the water circulating in a closed loop hydronic system. This does not add up…unless there is a major leak! So, where did the water go?
In addition to leaving the Testing, Adjusting, and Balancing (TAB) team unable to continue, if left unattended, the problem would lead to wasted energy and unstable room temperature control.
Let us look at the where and what followed by the how and why?
Where:
The new five floor residence building consisted of three floors above grade containing 302 hotel rooms, with the two floors below grade consisting of a full basement and a full cellar. A five floor core section, linked the three Y shaped building together, which was implemented in three project phases; Fan-coils equipped with a hydronic chilled water and heating hot water supplied HVAC to each room.
What:The mechanical contractor installed and started the hydronic (CHW pump, tanks, valves, etc.) and HVAC equipment. The TAB team measured the CHW pump performance. Everything was fine up to this point. The TAB project scope involved differential pressure readings of the CHW automatic flow limiting balancing valves (FLVs) on the 350 fan-coil units and 6 air-handling units. The CHW pump differential pressure (DP, ΔP) setpoint was set to reach a minimum of 2.0 ΔP at the FLV on the worst-case unit. This allows for efficient system operation and better room temperature control.
Let us go over to a technical detail for a moment. The CHW pump circulating the water ran at the nameplate motor amperage which indicated the pump is running more or less as expected. However, several CHW FLVs installed on fan-coil units measured less than the minimum required pressure drop of 2.0 ΔP mentioned earlier to confirm design CHW waterflow.
The numbers did not add up: The CHW pump performance data reflected design CHW waterflow and the fan-coil units indicated not enough waterflow.
How & Why
How and why did this happen? Troubleshooting does not always mean looking for a needle in a haystack. We started with a simple “could be/no way” list approach. This is a process where we first cut out the obvious “no way” issues and then progressively eliminate other possible issues. This process also included comparing this system to one that is working properly.
No Way...
- Electrical issue? No way. This is mechanical in nature.
- System leak? A leak would show up with water puddling on the floor or flooding. In addition, the make-up water meter would show water entering the system to make-up for water leaving the system.
- Could you add to the “No way” list?
Could it Be...
- A pump rotation issue? A pump spinning backwards may still show waterflow and positive pressure. The Cx team did not want to assume, so we verified the pump rotation again.
- The hydrometer used to take the readings? The hydrometer used to measure the CHW pressure differential had a very recent calibration certification from the manufacturer. However, the TAB team used a different calibrated meter to eliminate a faulty meter from the equation.
- Inaccurate pump performance data? To verify the waterflow determined when using the pump curve, the team used an ultrasonic strap on the meter. The flow from the ultrasonic meter and the pump curve matched within 5%! In addition, the system’s flow transmitter was also within an acceptable percentage of the pump curve and ultrasonic meter.
- Piping distribution issues? Could be! Perhaps a bypass valve?
- Fan-coil hydronic component issues? Should we trust the FLV pressure measurement? What issues could result from a faulty fan-coil hydronic component?
The team used the same forensic tool for the piping distribution and individual fan-coil unit troubleshooting: Differential static pressure profile.
The team prepared a system piping diagram based on the mechanical drawing piping detail. The pressure readings were noted on the diagram to see the big picture on one page. The testing started by measuring the differential pressure between the return and supply pipe mains using the pipe pressure-temperature access ports. Due to installation, pressure ports needed to be installed on certain riser drain locations as a temporary measure to record the differential pressure across the riser return and supply pipes. Looking at the big picture, it added up!
The pressure drops across the fan-coil unit cooling control valve and cooling coil both showed well above design waterflow on certain units and low waterflow on other units. We are getting warm. Why was the pressure drop across the FLV exceptionally low on these units showing above design waterflow across the cooling coil? What could cause a FLV to have above design waterflow but below design pressure drop? The question is how to go from “could be” to “this is it”?
An inspection of the FLVs revealed that the manufacturer placed the flow direction sticker in the wrong direction on a batch of FLVs, resulting in the FLV being installed backwards. Once the FLV reversed to the correct direction, the pressure drop reached the required 2.0 ΔP.
The head scratcher continued! Although certain FLVs were installed in the correct direction, the pressure drops on other FLVs indicated low pressure drop with above normal pressure drop across the cooling coil. We put the FLV under the Cx microscope by disassembling it. [See image below].
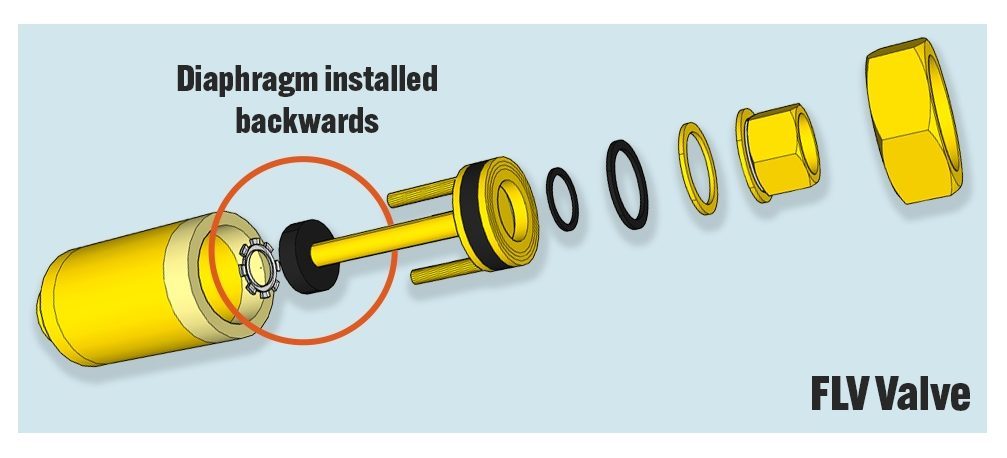
The rubber diaphragm is position sensitive and when installed backwards or even missing forces, the valve will wide open with flow or allows for full flow through the valve; hence the low pressure drops although lots of water is moving through the FLV. The rubber diaphragm was removed prior to soldering but installed backwards or never reinstalled in some cases during the installation process. The install team corrected the issue by following the FLV Installation, Operation, and Maintenance Manual (IOM) install procedures to wrap the valve body with a wet rag.
What can we take away from a system operation that did not add up?
- Quality Assurance is a fundamental part of the construction process and includes following the procedures outlined in the equipment and IOM Manuals. The manufacturer detailed a solution to the valve soldering issue in the IOM Manual. On the other hand, the misplaced FLV direction sticker was a Quality Control issue beyond the project.
- TAB is indispensable during the construction project. In addition to helping with energy conservation and temperature control, TAB is a troubleshooting and mechanical system health tool. As a result, our Cx team TAB report review occurs before the functional testing phase.
- Troubleshooting should not involve looking for a needle in a haystack. The Cx team which included the mechanical and TAB contractors dissected system to narrow down the issue using actual system measurements. Viewing the system pressures at each major connection in the system and across each fan-coil component allowed us to focus our efforts on the real cause in less time.
Once it all added up, the CHW system was balanced, energy payback rebates were set in motion, and the cooling system delivered stable temperature control to the spaces.