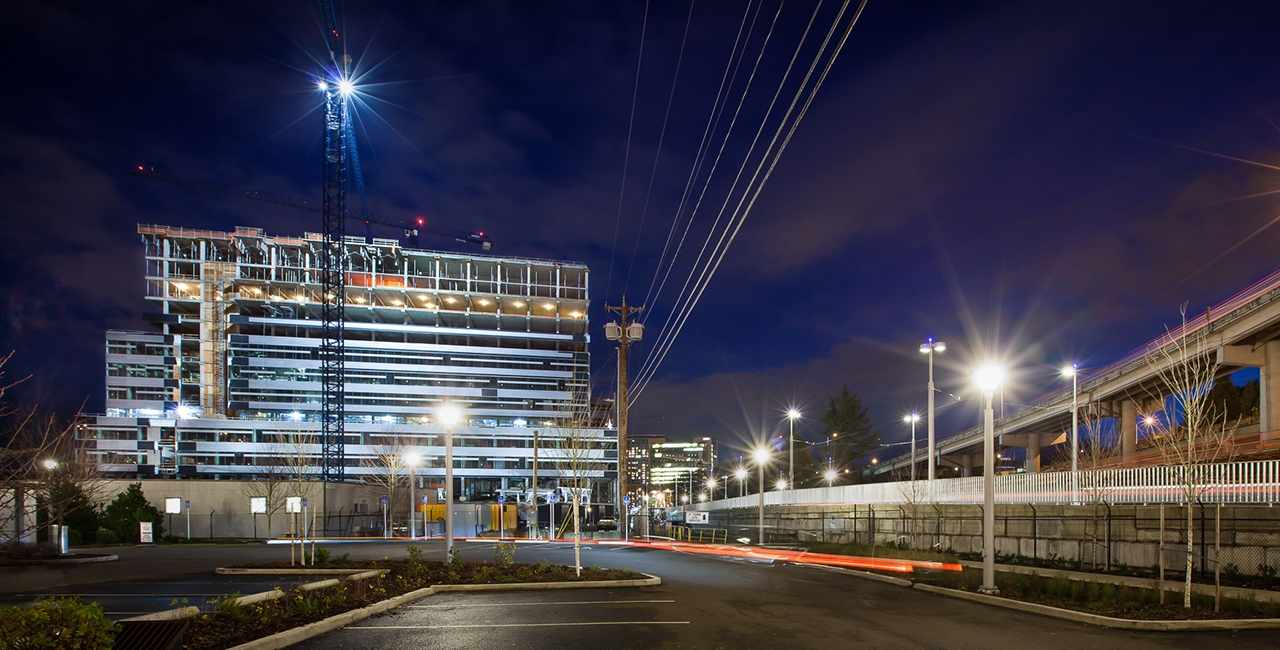
Alene Davis
The Importance of BIM and Efficient Laboratory Systems
Case Study
Oct 03, 2014
by John McMichael, PE and Wade Snyder, JE Dunn Construction
School is truly back in at OHSU’s recently completed Collaborative Life Sciences Building. The building, along with Skourtes Tower, is the result of a joint venture between Portland State University, Oregon State University, and Oregon Health & Science University, and is designed to foster collaboration among students and instructors from the multiple institutions.
The recently LEED Platinum Certified buildings include simulation, teaching, and research labs; retail space; offices; classrooms; multiple lecture halls; and a 200-chair dental school. The completion was made possible on a very short timeline using advanced Building Information Management (BIM) techniques.
Without such a plan, the design team could not have accomplished:
- 650,000 square feet (including garage)
- $295 million construction cost
- 32 months design/construction timeframe
- Up to 500 workers onsite at once
- 45% energy savings
- 26 miles of plumbing systems
- 126 miles of conduit
- LEED Platinum Certification
Jeremy Bitterman Photography
Building Information Management Techniques
Creation of the building model provided consistent data for wind dispersion analysis, smoke control and life safety calculations, energy modeling, lighting calculations, and HVAC loads. This model was used by the contractor to set sleeves and anchors for a multitude of service pipes and ducts. Because the fast pace dictated that there was overlap of design and construction, the model delivered real time coordination of trades. “Lockdown” of design at systematic intervals permitted designers to contribute useful information up to the last minute. Concepts were vetted in real time because of the early BIM modeling and colocation of team members (Owner, Contractor, Architect, Engineers).
The use of a heat recovery chiller and the strategic integration of how the systems are laid out allow significant savings on the heating bills. Cooling is enhanced by careful selection of chillers. Fan static pressure is decreased by use of dual purpose heating/cooling coils. This lowers operating costs significantly since the laboratory fans run 24/7. Use of multiple small plenum fans in air handlers saved space and provided more program area in a smaller building footprint. Evaporative humidification supplied with heat by the heat recovery chiller gave the Vivarium a humidification system with a very high heating Coefficient of Performance (5.0).
Use of the BIM model translates design information to the field electronically in the form of construction coordinates. The process once automated, increased speed of layout. In spite of the complexity of floor penetrations for piping, ductwork and conduit, large sections of floor slabs were poured at two week intervals. The BIM model should prove to be a resource for ongoing operations and maintenance, as well as future renovations over the life of the building.
Other construction practices used to save time and improve quality included prefabrication of pipe racks carrying domestic water, hot/cold, dental vacuum, and lab gases. Once the racks were brought to the job site, hoisting and horizontal transport to the installation were carried out at a rapid pace. The time from crane lift to completed rack hanging from the slab was a matter of two to four hours. By fabricating offsite and scheduling just-in-time delivery it is estimated the project saved 15% compared to onsite fabrication.
Other BIM related practices included jobsite kiosks with full access to the contractor’s current record set at all times. This full tracking of RFI’s, drawings, and submittals allowed questions about the complexity of construction to be visualized and answered in an efficient manner. The organization of data was paramount since documentation equated to having one drawing being issued every six minutes on the project. It was estimated that $1.5 million in printing costs alone were saved by this approach.